Lavorazione di taglio di parti di metallurgia delle polveri (P/M)
L'uso del processo di metallurgia delle polveri (P / M) per la produzione di parti per sistemi di alimentazione automobilistica continua a crescere. Le parti prodotte dal processo P / M hanno molti vantaggi importanti e unici. La struttura porosa residua lasciata intenzionalmente in queste parti è ottima per l'autolubrificazione e l'isolamento acustico. Le leghe complesse che sono difficili o impossibili da produrre con il processo di fusione tradizionale possono essere prodotte utilizzando la tecnologia P/M. Le parti prodotte con questa tecnologia di solito hanno poca o nessuna capacità di elaborazione, il che le rende più economiche e con meno sprechi di materiali. Sfortunatamente, dietro l'attrazione di queste caratteristiche, le parti P / M sono difficili da lavorare.
Sebbene una delle intenzioni originarie dell'industria P/M sia quella di eliminare tutte le lavorazioni, questo obiettivo non è stato ancora raggiunto. La maggior parte delle parti può essere solo "vicina alla forma finale" e necessita ancora di una rifinitura.
Tuttavia, rispetto a pezzi fusi e forgiati, una piccola quantità di materiale che deve essere rimossa dalle parti P/M è un tipico materiale resistente all'usura.
La struttura porosa è una delle caratteristiche che rendono le parti p / M hanno una vasta gamma di usi, ma anche la vita dell'utensile sarà danneggiata dalla struttura porosa. La struttura porosa può immagazzinare olio e suono, ma porta anche a micro tagli intermittenti. Quando ci si sposta avanti e indietro dal foro alle particelle solide, la punta dell'utensile viene continuamente urtata, il che può portare a una deformazione da frattura per fatica molto piccola e al collasso del bordo sottile lungo il tagliente. A peggiorare le cose, le particelle di solito sono molto dure. Anche se la macrodurezza del materiale misurato è compresa tra 20 e 35 gradi, la dimensione delle particelle del componente raggiunge i 60 gradi. Queste particelle dure causano un'usura dei bordi grave e rapida. Molte parti p / M sono trattabili termicamente e la durezza e la resistenza del materiale sono maggiori dopo il trattamento termico. Infine, a causa della tecnologia di sinterizzazione e trattamento termico e dei gas utilizzati, la superficie del materiale conterrà ossidi e/o carburi duri e resistenti all'usura.
Prestazioni delle parti P/M
La maggior parte delle proprietà delle parti P/M, inclusa la lavorabilità, sono legate non solo alla composizione chimica della lega, ma anche al livello di porosità della struttura porosa. La porosità di molte parti strutturali è fino al 15% ~ 20%. La porosità delle parti utilizzate come dispositivi di filtrazione può raggiungere il 50%. All'altra estremità della serie, la porosità delle parti forgiate o dell'anca è solo dell'1% o meno. Questi materiali stanno diventando particolarmente importanti nelle applicazioni automobilistiche e aeronautiche perché possono raggiungere livelli di resistenza più elevati.
La resistenza alla trazione, la tenacità e la duttilità della lega P/M aumenteranno con l'aumento della densità e anche la lavorabilità potrebbe essere migliorata, poiché la porosità è dannosa per la punta dell'utensile.
L'aumento del livello di porosità può migliorare le prestazioni di isolamento acustico delle parti. L'oscillazione di smorzamento nelle parti standard è significativamente ridotta nelle parti P / M, che è molto importante per macchine utensili, cannelli di aria condizionata e utensili pneumatici. L'elevata porosità è necessaria anche per gli ingranaggi autolubrificanti.
Difficoltà nella lavorazione
Sebbene uno degli obiettivi del continuo sviluppo dell'industria P/M sia quello di eliminare la lavorazione, e una delle principali attrazioni del processo P/M è che è necessaria solo una piccola quantità di lavorazione, molte parti necessitano ancora di post-trattamento per ottenere maggiore precisione o migliore finitura superficiale. Sfortunatamente, la lavorazione di queste parti è estremamente difficile. La maggior parte dei problemi riscontrati sono causati dalla porosità. La porosità porta alla micro fatica del tagliente. Il tagliente taglia costantemente dentro e fuori. Passa tra particelle e buchi. Un piccolo impatto ripetuto porta a piccole crepe sul tagliente.
Queste crepe da fatica crescono fino a quando il tagliente non collassa. Questo tipo di bordo a microscheggiatura è solitamente molto piccolo e di solito mostra una normale usura abrasiva.
La porosità riduce anche la conduttività termica delle parti P/M, che si traduce in un'elevata temperatura sul tagliente e provoca craterizzazione e deformazione. La struttura porosa collegata internamente fornisce un percorso per lo scarico del fluido da taglio dall'area di taglio. Ciò può causare crepe o deformazioni a caldo, specialmente durante la perforazione.
L'aumento di superficie causato dalla struttura porosa interna porta anche all'ossidazione e/o alla carbonizzazione durante il trattamento termico. Come accennato in precedenza, questi ossidi e carburi sono duri e resistenti all'usura.
La struttura porosa fornisce anche il fallimento della lettura della durezza del pezzo, che è estremamente importante. Quando la macro durezza di un pezzo P/M viene misurata intenzionalmente, include il fattore di durezza del foro. La struttura porosa porta al collasso della struttura e dà l'impressione sbagliata di parti relativamente morbide. Le particelle sono molto più dure. Come descritto sopra, la differenza è drammatica.
Anche l'esistenza di inclusioni nelle parti in PM è svantaggiosa. Durante la lavorazione, queste particelle verranno sollevate dalla superficie e si formeranno graffi o graffi sulla superficie del pezzo quando viene sfregato davanti all'utensile. Queste inclusioni sono generalmente grandi, lasciando fori visibili sulla superficie della parte.
La differenza del contenuto di carbonio porta all'incoerenza della lavorabilità. Ad esempio, il contenuto di carbonio della lega fc0208 varia dallo 0.6% allo 0.9%. Un lotto di materiali con un contenuto di carbonio dello 0.9% è relativamente duro, con conseguente scarsa durata dell'utensile. L'altro lotto di materiali con contenuto di carbonio dello 0.6% ha un'eccellente durata dell'utensile. Entrambe le leghe rientrano nell'intervallo consentito.
Il problema della lavorazione finale è legato al tipo di taglio che avviene sul pezzo P/M. Poiché la parte è vicina alla forma finale, la profondità di taglio è generalmente molto ridotta. Ciò richiede un tagliente libero. L'accumulo di trucioli sul tagliente spesso porta a microscheggiature.
Tecnologia di elaborazione
Per superare questi problemi, vengono applicate diverse tecnologie (uniche nel settore). La struttura porosa superficiale è spesso sigillata per infiltrazione. Di solito è necessario un ulteriore taglio libero. Recentemente sono state utilizzate tecniche di produzione di polvere migliorate progettate per aumentare la pulizia della polvere e ridurre ossidi e carburi durante il trattamento termico.
La struttura porosa a superficie chiusa è ottenuta mediante infiltrazione di metallo (solitamente rame) o polimero. È stato ipotizzato che l'infiltrazione agisca come lubrificante. La maggior parte dei dati sperimentali mostra che il vero vantaggio risiede nel chiudere la struttura porosa superficiale e prevenire così la micro fatica del tagliente. La riduzione delle vibrazioni migliora la durata dell'utensile e la finitura superficiale. L'uso più drammatico dell'infiltrazione mostra un aumento del 200% della durata dell'utensile quando la struttura porosa è chiusa.
È noto che additivi come MNS, s, MoS2, MgSiO3 e BN aumentano la durata dell'utensile. Questi additivi migliorano la lavorabilità facilitando la separazione dei trucioli dal pezzo, la rottura dei trucioli, la prevenzione della formazione di trucioli e la lubrificazione del tagliente. L'aumento della quantità di additivi può migliorare la lavorabilità, ma ridurre la resistenza e la tenacità.
La tecnologia di atomizzazione della polvere per controllare la sinterizzazione e il gas del forno di trattamento termico consente di produrre polvere e parti pulite, riducendo al minimo la presenza di inclusioni e carburi di ossido superficiale.
Materiale per utensili
Gli utensili più utilizzati nell'industria P/M sono quei materiali che sono resistenti all'usura, alle crepe sui bordi e privi di scheggiature a condizione di una buona finitura superficiale. Queste caratteristiche sono utili per qualsiasi operazione di lavorazione, soprattutto per i pezzi P/M. I materiali per utensili inclusi in questa categoria sono utensili in nitruro di boro cubico (CBN), cermet rivestiti e non rivestiti e carburi cementati sinterizzati rivestiti migliorati.
Gli utensili in CBN sono attraenti per la loro elevata durezza e resistenza all'usura. Questo strumento è stato utilizzato per molti anni nella lavorazione di acciaio e ghisa con durezza Rockwell di 45 e oltre. Tuttavia, a causa delle proprietà uniche della lega P/M e della differenza significativa tra microdurezza e macrodurezza, gli utensili CBN possono essere utilizzati per parti P/M con durezza Rockwell di 25. Il parametro chiave è la durezza delle particelle. Quando la durezza delle particelle supera i 50 gradi Rockwell, gli utensili CBN sono disponibili indipendentemente dal valore di macro durezza. L'ovvio limite di questi strumenti è la loro mancanza di robustezza. In caso di taglio intermittente o elevata porosità, è necessario un rinforzo del bordo che includa smussatura negativa e levigatura pesante. Il taglio leggero semplice può essere eseguito con il tagliente levigato.
Ci sono diversi materiali di CBN che sono efficaci. Il materiale con la migliore tenacità è composto principalmente dall'intero CBN. Hanno un'ottima tenacità, quindi possono essere utilizzati per la sgrossatura. I loro limiti sono solitamente legati alla finitura superficiale. È in gran parte determinato dalle singole particelle di CBN che compongono lo strumento. Quando le particelle cadono dal tagliente, influenzeranno la superficie del materiale del pezzo. Tuttavia, non è così grave che lo strumento per particelle fini cada da una particella.
Il materiale CBN solitamente utilizzato ha un alto contenuto di CBN e una granulometria media. La lama di finitura CBN è a grana fine e il contenuto di CBN è basso. Sono più efficaci quando sono richiesti un taglio leggero e una finitura superficiale o quando la lega in lavorazione è particolarmente dura.
In molte applicazioni di taglio, la durata dell'utensile è indipendente dal tipo di materiale. In altre parole, qualsiasi materiale CBN può raggiungere una durata utensile simile. In questi casi la scelta del materiale si basa principalmente sul minor costo di ogni tagliente. Una lama rotonda ha un'intera superficie superiore in CBN e può fornire quattro o più taglienti, il che è più economico di quattro lame CBN intarsiate.
Quando la durezza delle parti P / M è inferiore a 35 gradi Rockwell e la durezza delle particelle rientra nell'intervallo, il cermet è solitamente una delle scelte. I cermet sono molto duri, possono prevenire efficacemente l'accumulo di trucioli e possono resistere alle alte velocità. Inoltre, poiché i cermet sono sempre stati utilizzati per la lavorazione ad alta velocità e di finitura di acciaio e acciaio inossidabile, di solito hanno scanalature geometriche ideali adatte a parti vicine alla forma.
I cermet odierni sono intricati nella metallurgia, con un massimo di 11 elementi di lega. Di solito sono sinterizzati da particelle di TiCN e adesivo Ni Mo. TiCN fornisce durezza, resistenza alla formazione di trucioli e stabilità chimica che sono importanti per il successo dell'uso dei cermet. Inoltre, questi strumenti di solito hanno un alto contenuto di adesivo, il che significa che hanno una buona tenacità. In una parola, hanno tutte le caratteristiche per lavorare efficacemente la lega P/M. Diversi tipi di cermet sono efficaci, proprio come il carburo cementato sinterizzato con carburo di tungsteno, maggiore è il contenuto di legante, migliore è la tenacità.
Un noto sviluppo relativamente nuovo è che la deposizione chimica da vapore a media temperatura (mtcvd) fornisce anche un vantaggio per l'industria P/M. Mtcvd mantiene tutta la resistenza all'usura e alla craterizzazione della tradizionale deposizione chimica da vapore (CVD), ma migliora anche oggettivamente la tenacità. L'aumento della tenacità deriva principalmente dalla diminuzione delle cricche. Il rivestimento viene depositato ad alta temperatura e poi raffreddato in forno. Il rivestimento contiene crepe quando l'utensile raggiunge la temperatura ambiente a causa dell'espansione termica incoerente. Simili ai graffi sul vetro piano, queste crepe riducono la resistenza del tagliente. La temperatura di deposizione più bassa di mtcvd porta a una frequenza di cricca più bassa ea una migliore tenacità del tagliente.
Quando il substrato del rivestimento CVD e del rivestimento mtcvd hanno le stesse caratteristiche e la stessa ravvivatura dei bordi, è possibile dimostrare la differenza della loro tenacità. Quando viene utilizzato in applicazioni in cui è richiesta la tenacità del tagliente, le prestazioni del rivestimento mtcvd sono migliori di quelle del rivestimento CVD. Attraverso l'analisi, quando si lavorano parti P/M con struttura porosa, la tenacità del tagliente è importante. Il rivestimento Mtcvd è migliore del rivestimento CVD.
Il rivestimento di deposizione fisica da vapore (PVD) è più sottile e meno resistente all'usura rispetto al rivestimento mtcvd o CVD. Tuttavia, il rivestimento PVD può resistere a un impatto significativo nell'applicazione. Il rivestimento PVD è efficace quando il taglio è soggetto a usura abrasiva, CBN e cermet sono troppo fragili e richiedono un'eccellente finitura superficiale.
Ad esempio, il tagliente in metallo duro C-2 può essere lavorato fc0205 a una velocità di linea di 180 m/min e una velocità di avanzamento di 0.15 mm/giro. Dopo la lavorazione di 20 parti, l'accumulo di trucioli può causare un micro collasso. Quando si utilizza il rivestimento PVD in nitruro di titanio (TIN), l'accumulo di truciolo viene limitato e la durata dell'utensile è prolungata. Quando viene utilizzato il rivestimento di stagno per questo test, le caratteristiche di usura abrasiva delle parti P / M dovrebbero essere più efficaci con il rivestimento TiCN. Il TiCN ha quasi la stessa resistenza all'accumulo di trucioli dello stagno, ma è più duro e resistente all'usura dello stagno.
La struttura porosa è importante e influisce sulla lavorabilità della lega fc0208. Quando la struttura porosa e le caratteristiche cambiano, i diversi materiali degli utensili offrono vantaggi corrispondenti. Quando la densità è bassa (6.4 g/cm3), la macrodurezza è bassa. In questo caso, il metallo duro con rivestimento mtcvd offre la migliore durata dell'utensile. La micro fatica del tagliente è molto importante e la tenacità del tagliente è molto importante. In questo caso, una lama in cermet di buona tenacità garantisce la massima durata dell'utensile.
Quando si produce la stessa lega con una densità di 6.8 g/cm3, l'usura abrasiva diventa più importante della rottura del bordo. In questo caso, il rivestimento mtcvd offre la migliore durata dell'utensile. Il carburo cementato rivestito in PVD viene utilizzato per testare i due tipi di parti estremamente dure e si rompe quando tocca il tagliente.
Quando la velocità aumenta (la velocità lineare è superiore a 300 metri al minuto), i cermet e anche i cermet rivestiti producono crateri. Il metallo duro rivestito è più adatto, specialmente quando la tenacità del tagliente del metallo duro rivestito è buona. Il rivestimento Mtcvd è particolarmente efficace per il carburo cementato con un'area ricca di cobalto.
I cermet sono più comunemente usati nella tornitura e nella foratura. I carburi cementati rivestiti in PVD sono ideali per la lavorazione di filettature perché ci si possono aspettare velocità inferiori e maggiore attenzione all'accumulo.
Si prega di conservare la fonte e l'indirizzo di questo articolo per la ristampa:Lavorazione di taglio di parti di metallurgia delle polveri (P/M)
Minghe Casting Company si dedica alla produzione e alla fornitura di parti di colata di qualità e ad alte prestazioni (la gamma di parti di pressofusione di metalli comprende principalmente Pressofusione a parete sottile,Pressofusione a camera calda,Pressofusione a camera fredda), servizio rotondo (servizio di pressofusione,Lavorazione cnc,Costruzione di stampi, Trattamento della superficie). Qualsiasi pressofusione di alluminio personalizzata, magnesio o pressofusione di zama/zinco e altri requisiti di getti sono invitati a contattarci.
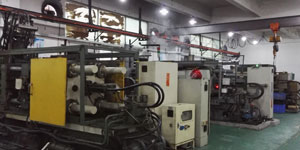
Sotto il controllo di ISO9001 e TS 16949, tutti i processi vengono eseguiti attraverso centinaia di macchine per pressofusione avanzate, macchine a 5 assi e altre strutture, che vanno dai blaster alle lavatrici Ultra Sonic. Minghe non solo dispone di attrezzature avanzate ma anche di professionisti team di ingegneri esperti, operatori e ispettori per realizzare il progetto del cliente.
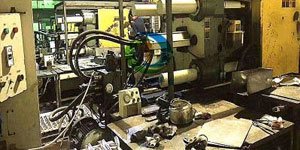
Produttore conto terzi di pressofusioni. Le capacità includono parti in pressofusione di alluminio a camera fredda da 0.15 libbre. a 6 libbre, impostazione del cambio rapido e lavorazione. I servizi a valore aggiunto includono lucidatura, vibrazione, sbavatura, granigliatura, verniciatura, placcatura, rivestimento, assemblaggio e lavorazione con utensili. I materiali lavorati includono leghe come 360, 380, 383 e 413.
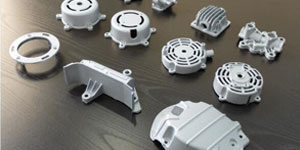
Assistenza alla progettazione di pressofusione di zinco/servizi di ingegneria concorrente. Produttore personalizzato di pressofusioni di zinco di precisione. È possibile produrre fusioni in miniatura, pressofusioni ad alta pressione, fusioni multi-slitta, fusioni in conchiglia convenzionali, pressofuse unitarie e indipendenti e fusioni a cavità sigillata. I getti possono essere prodotti in lunghezze e larghezze fino a 24 pollici con una tolleranza di +/- 0.0005 pollici.
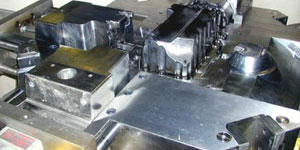
Produttore certificato ISO 9001:2015 di pressofusione di magnesio, le funzionalità includono pressofusione di magnesio ad alta pressione fino a 200 tonnellate di camera calda e 3000 tonnellate di camera fredda, progettazione di utensili, lucidatura, stampaggio, lavorazione, verniciatura a polvere e liquida, controllo di qualità completo con funzionalità CMM , montaggio, imballaggio e consegna.
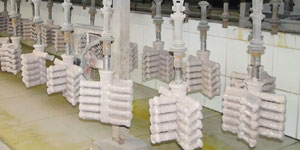
Certificato ITAF16949. Il servizio di casting aggiuntivo include colata di investimento,colata in sabbia,Colata per gravità, Colata di schiuma persa,Colata centrifuga,Colata sotto vuoto,Colata in stampo permanente,.Le funzionalità includono EDI, assistenza ingegneristica, modellazione solida ed elaborazione secondaria.
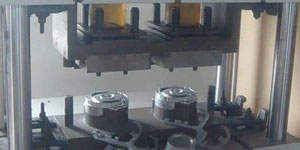
Industrie di colata Casi di studio di parti per: automobili, biciclette, aerei, strumenti musicali, imbarcazioni, dispositivi ottici, sensori, modelli, dispositivi elettronici, custodie, orologi, macchinari, motori, mobili, gioielli, maschere, telecomunicazioni, illuminazione, dispositivi medici, dispositivi fotografici, Robot, sculture, apparecchiature audio, attrezzature sportive, utensili, giocattoli e altro ancora.
Cosa possiamo aiutarti a fare dopo?
∇ Vai alla home page per Pressofusione Cina
→Parti di fusione-Scopri cosa abbiamo fatto.
→Suggerimenti correlati su Servizi di pressofusione
By Minghe produttore di pressofusione |Categorie: Articoli utili |Materiali Tag: Fusione di alluminio, Colata di zinco, Colata di magnesio, Colata di titanio, Colata in acciaio inossidabile, Fusione di ottone,Fusione in bronzo,Cast video,Storia dell'azienda,Pressofusione di alluminio |Commenti disabilitati